
シェルモールド法の工程やメリット・デメリットを解説
シェルモールド法の特徴や工程とは?メリット・デメリットも解説
製造業において、高品質な製品を効率的に生産することは重要な課題です。その中で、シェルモールド法は注目を集める鋳造技術の一つとなっています。この技術は、他の鋳造法と比べて多くの利点を持っています。
こちらでは、シェルモールド法の特徴や具体的な工程、メリット・デメリットを詳しく解説します。シェルモールド法の可能性と課題を探り、より効果的な製造プロセスの構築にお役立ていただければ幸いです。
シェルモールド法の特徴
シェルモールド法は、精密で高品質な鋳物を効率的に生産するための鋳造技術です。この方法は、熱硬化性樹脂を含む特殊な砂・RCS(レジンコーテッドサンド)を使用して薄い殻状の鋳型を作成することが特徴です。
1944年にドイツのヨハネス・クローニング博士によって開発されたこの技術は、当時の産業界に革命をもたらしました。その後、技術の改良と設備の進化により、現在では自動車部品や水栓金具など、様々な分野で広く活用されています。
シェルモールド法による中子製造の工程
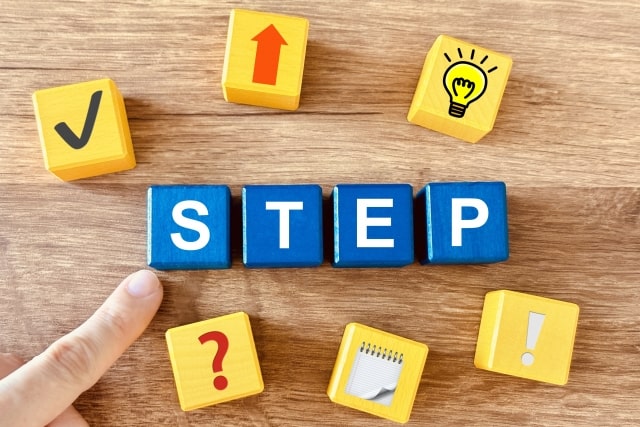
シェルモールド法の工程は、精密な鋳造品を効率的に生産するために最適化されています。シェルモールド法における中子製造の工程は、以下のような流れで進められます。
1.砂の充填
最初に、加熱された中子製作用の型にRCS(レジンコーテッドサンド)加圧噴射して充填します。RCSは、熱硬化性樹脂でコーティングされた特殊な砂です。
2.焼成プロセス
充填後、250~300℃程度に加熱した、RCSを硬化させます。この工程を焼成と呼びます。さらに、反転焼成を行うことで外側の砂だけを残し、内部の砂を排出します。これにより二枚貝の殻(シェル)のような中空構造が形成され、軽量化とコスト削減が実現します。
3.中子の取り出し
焼成が完了したら、型を開いて硬化した中子を取り出します。
4.仕上げ作業
取り出した中子に対して、必要に応じて以下のような仕上げ作業を行います。
- バリ取り:中子表面の不要な突起物を除去
- 塗型:溶湯の熱から中子を保護し、ガスの発生を抑制
- 二次焼成:残留水分の除去とガス発生の防止
5.鋳造工程への移行
仕上げが完了した中子は、通常の鋳造工程に組み込まれます。具体的には、主型へのセット、注湯、主型の解体、そして最後に中子の除去という流れで進行します。
このように、シェルモールド法による中子製造は、高精度かつ効率的な鋳造プロセスを実現する重要な工程となっています。
シェルモールド法のメリット
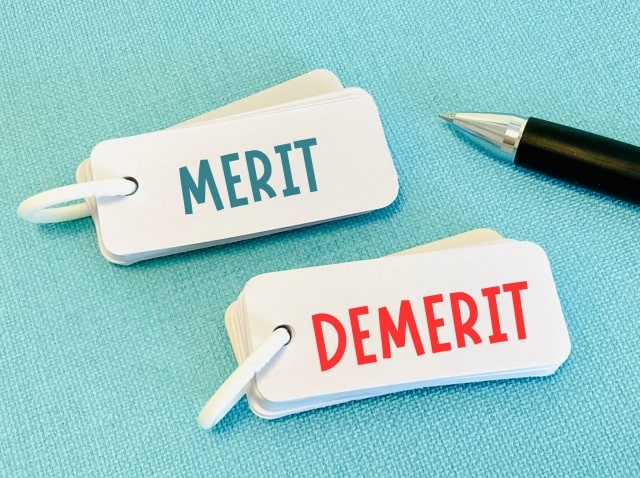
シェルモールド法には、他の鋳造法に比べて多くのメリットがあります。主な利点として以下が挙げられます。
高精度な鋳造が可能
シェルモールド法は、砂型鋳造でありながら金型鋳造に匹敵する高い寸法精度を実現できる鋳造技術です。この優れた精度は、主に高い強度に起因しています。シェルモールド法の工程で作られた鋳型は強度が高く、金属の膨張にも耐えられるため、通常の砂型鋳造の工程と比較して寸法精度が高くなります。
この高強度・高精度の特性を活かし、シェルモールド法は特に精密さが要求される製品の製造工程に広く採用されています。代表的な応用例として、自動車部品が挙げられます。これらの部品は特に精密さが求められるため、シェルモールド法の特性が最大限に発揮されます。
シェルモールド法は従来の砂型鋳造の利点を保ちつつ、金型鋳造に迫る精度を実現する方法として、精密部品の製造業界で重要な役割を果たしています。
表面仕上げの品質が高い
シェルモールド法は、表面仕上げの品質が非常に高いことで知られています。シェルモールド法の工程で製造された鋳物は滑らかで均一な表面を持ち、鋳肌が美しく仕上がります。特に、複雑な形状や薄肉の部品製造において、その高い表面品質が活かされています。
また、この優れた表面仕上げ品質は製品の外観だけでなく、機能性にも大きく寄与します。例えば、自動車エンジン部品や精密機械部品など、高い寸法精度や表面品質が要求される製品に適しています。
大量生産に適している
シェルモールド法の工程は、大量生産に非常に適した鋳造方法です。鋳型の製作が容易なので、同一形状の製品を短時間で大量に生産することが可能となります。
また、シェルモールド法は鋳鉄、アルミニウム、銅など、幅広い種類の材料に対応しています。そのため、様々な製品の大量生産に適用することができます。
金型を使用するため初期の投資は必要ですが、大量生産により長期的には非常にコスト効率の良い生産方法となります。シェルモールド法は自動車部品や電気機器部品など、同一形状の製品を大量に必要とする産業分野で広く活用されています。
保存・管理のしやすさ
シェルモールド法の大きな利点として、保存・管理のしやすさが挙げられます。吸湿性が低く、乾燥状態を長期間維持することができます。さらに高い強度を持っているため、長距離の輸送にも耐えることができます。
これにより製造拠点と使用場所が離れている場合なども、品質を損なうことなく効率的な生産・供給が可能となります。このような保存・管理のしやすさは、在庫管理の効率化やコスト削減にもつながります。
シェルモールド法のデメリット
シェルモールド法は高精度な鋳造が可能な優れた手法ですが、いくつかの課題も抱えています。主なデメリットは以下のとおりです。
初期設備投資が高い
シェルモールド法は、初期設備投資が高くなる傾向があります。その主な理由として、金型の使用が挙げられます。シェルモールド法の工程では、高温に耐える専用の金型が必要不可欠です。また、金型を高温で繰り返し加熱する必要があるため、金型の耐用年数が他の鋳造法と比べて短くなります。そのため金型にかかるコストが増加し、初期投資額を押し上げる結果となります。
シェルモールド法の導入を検討する際は、これらの初期投資コストと、生産性向上や品質改善によるメリットを慎重に比較検討することが重要です。特に、生産数量や製品の複雑さ、要求される精度などを考慮し、総合的な判断を行う必要があります。
大型鋳物には不向き
シェルモールド法は多くの利点を持つ優れた鋳造法ですが、大型の鋳物製造にはあまり適していません。シェルモールド法は主に小型から中型の鋳物製造に適しており、大型鋳物の製造には他の鋳造法が選択されることが多いです。製品の大きさや形状、必要な精度、生産量などを考慮し、最適な鋳造法を選択することが重要です。
シェルモールド法は、その特性を活かせる適切なサイズの製品製造において、高い効率性と品質を発揮します。
これらのデメリットを克服するため、各企業では設備の改良や作業環境の整備、新技術の開発などに取り組んでいます。コスト削減や生産性の向上を目指し、シェルモールド法のさらなる進化が期待されています。
シェルモールド法によるシェル中子製造のご相談は岐鋳へ
シェルモールド法は、高品質な鋳造を可能にする技術です。強度が高く高精度な鋳造が可能、表面仕上げの品質が高い、大量生産に適しているなど、多くのメリットがあります。シェルモールド法は高い精度と高生産性を両立させた鋳造法であり、今後も製造業において重要な役割を果たしていくでしょう。
岐阜県山県市に拠点を置く岐鋳では、水栓金具のシェル中子製造を行っております。小回りの利く柔軟な対応力を活かし、大物を扱う製造会社では難しい小物の製作や小ロット生産が可能です。全国の法人様のニーズに応じた部品の製造を行っており、御社製品の品質向上や低コスト化に貢献いたします。ご相談やお見積もりのご依頼など、各種お問い合わせを受け付けております。どうぞお気軽にご連絡ください。
シェルモールド法の工程に関するお問い合わせは岐鋳まで
会社名 | 岐鋳 |
---|---|
住所 | 〒501-2115 岐阜県山県市梅原965 |
営業時間 | 9:00 – 17:00 |
定休日 | 土曜・日曜・祝日 |
TEL | 0581-27-0092 |
FAX | 0581-27-0093 |
事業内容 | 鋳造用シェル中子製造 |
URL | https://official-gichu.com/ |